Visite chez Gys, fleuron français du soudage
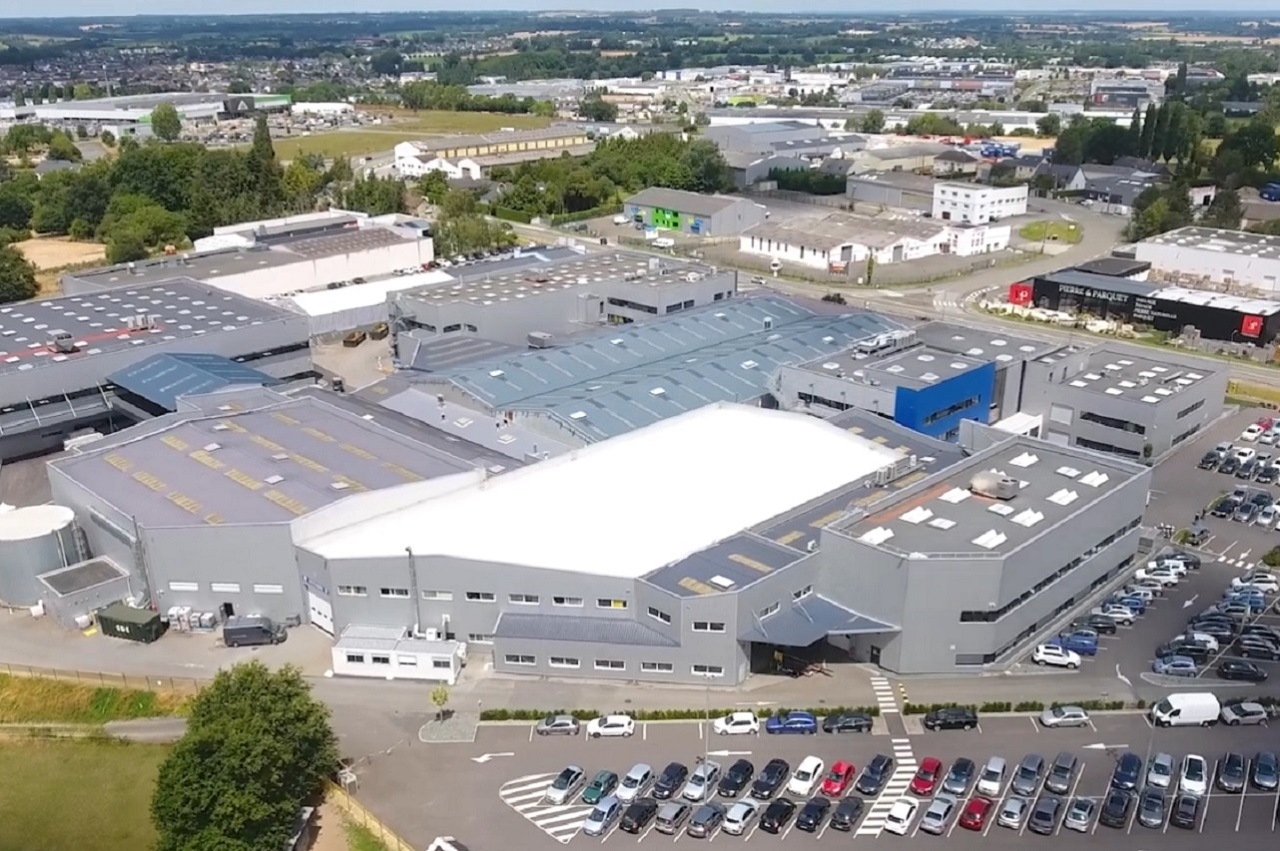
L’internalisation de la production est au cœur de la culture de Gys. Le nombre de ses sous-traitants reste le plus réduit possible. La délocalisation de ses fabrications est limitée et ses équipements de haute technologie sont toujours fabriqués en France. Sa stratégie repose sur l'innovation continue et l'indépendance technologique. Et cette position assumée n’a pas empêché le fabricant de se faire reconnaître comme l’un des meilleurs spécialistes mondiaux du soudage. Bien au contraire.
Développement international
En effet, plus de la moitié de son chiffre d’affaires de 130 millions d’euros est ainsi réalisé à l’international, dans 132 pays. Son cœur de métier historique, le soudage représente 40 % de son activité, à égalité avec celle de carrosserie (soudage, accessoires, débosselage, levage, servantes d'atelier, etc.). Enfin, sa partie plus récente d'entretien et de charge de batterie – y compris automobile – en représente 20 %.
"Nous ne fabriquons pas tout en France. Une partie est produite dans notre usine chinoise. Mais notre atout est d'entretenir nos compétences en interne", explique Bruno Bouygues. Le président du groupe Gys précise que "l'implantation d'une usine en Europe de l'Est fait partie de nos projets à moyen terme. Demain, il nous faudra ouvrir aussi un site en Inde. Mais nous restons d'abord Français et Européens". Le groupe compte ainsi cinq filiales, en Grande-Bretagne, en Allemagne, en Italie, en Espagne et en Chine. Dans ce dernier pays, il est à la fois présent pour le commerce de ses produits et la fabrication de petits équipements sans technologie sensible – des chargeurs "basiques" notamment.
Internalisation maximum
Les sous-composants électroniques utilisés par Gys proviennent de toute l'Asie. Mais ses énormes stocks lui ont permis d'atténuer les effets des crises sanitaires, logistiques et géostratégiques de ces dernières années. ©J2R/NG
C'est dans son immense usine de Laval qu'est fabriqué l'essentiel de ses équipements. Le siège historique de l'entreprise, fondée en 1958, accueille également son centre de recherches et développements. Celui-ci bénéficie du réinvestissement d'environ 10 % de son chiffre d'affaires. Tandis que son outil de production est constamment mis à jour, avec une enveloppe annuelle de dix à quinze millions d'euros…
À lire aussi : Gys lance une table de levage ergonomique et performante
Le fonctionnement de cette machine est spectaculaire. En effet, une partie de ses 680 salariés travaillent dans 40 000 m2 d'atelier. Une part importante de la production y est automatisée. L'internalisation des fabrications inclut celles des composants électroniques, jusqu'à la tôlerie et à la peinture. Les partenaires locaux sont privilégiés pour les quelques cas de sous-traitance. "Le choix de l'internalisation nous permet de garder un œil sur la qualité de nos produits", explique Rémi Harti, directeur du département carrosserie.
De plus en plus de robots
Les travaux de tôlerie de Gys – depuis ses postes à souder jusqu’à ses outils de levage – sont également internalisés. ©J2R/NG
En parcourant la vingtaine d'ateliers du site, on prend la mesure de la multitude des savoir-faire de ses salariés. Les machines leur laissent peu de place. "Nous sommes sans cesse obligés de pousser les murs", commente Rémi Harti. Trois lignes de production automatisées assurent une capacité de production de 250 000 cartes électroniques par an. Celles-ci représentent 90 % des besoins de l'entreprise en composants électroniques. Certaines tâches de finition et le contrôle qualité y sont toutefois encore effectués par des opérateurs bien humains.
Tropicalisation de l'électronique, tôlerie, carrosserie des multiples matériels fabriqués, peinture, assemblage… Dans les autres ateliers, on retrouve des dizaines d'ouvriers qualifiés. Leur rôle est de plus en plus confiné aux tâches à forte valeur ajoutée. Un nombre croissant de robots les assistent pour les tâches les plus pénibles et répétitives. Détail non négligeable : l'entretien des machines est également internalisé au maximum. Elles sont régulièrement modernisées comme en peinture. "Avant, il fallait quatre heures pour changer de couleur. Aujourd'hui, quinze minutes suffisent", précise Rémi Harti.
60 000 composants par machine
Le centre de formation de Gys présente une carrosserie multi-matériaux, désormais courante sur les véhicules récents. Ceux-ci introduisent une complexité croissante dans les travaux de soudage des carrossiers. ©J2R/NG
Le service de recherche et développement emploie plus de 80 spécialistes. Ils testent notamment l'emploi des équipements dans des conditions extrêmes, avec des simulations de différents climats… Mais aussi sur les différents réseaux électriques internationaux, de qualité variable. Ils assurent ainsi la robustesse et l’adaptabilité des produits dans n'importe quel environnement. Ces spécialistes assurent aussi la production des logiciels intégrés – la partie désormais la plus sensibles des machines. Ils conçoivent aussi des techniques de réparation automobile de plus en plus complexes. Celles-ci intègrent notamment la détection dynamique de la dureté des matériaux pour les structures de carrosserie. Gys dépose ainsi plus de 20 brevets par an. Ceux-ci permettent à la marque de rester en pointe sur ses spécialités.
À lire aussi : Gys facilite le débosselage avec son Airfix Draw Aligner
Ainsi, le matériel de soudage a connu de grandes évolutions en quelques décennies. "Les anciens postes à souder Mig pouvaient durer 15 à 20 ans. Mais ce n'est plus le cas des nouvelles technologies, qui embarquent maintenant beaucoup d'électronique. Nous sommes ainsi passés de 15 à 60 000 composants par machine, explique José Marthino, technico-commercial démonstrateur. Cette évolution nous est imposée par la loi qui pousse à réduire la consommation d'énergie, ainsi que par des fonctions de plus en plus complexes". Il serait toutefois encore possible d'atteindre une longévité de 20 ans pour une soudeuse actuelle, mais à condition de l'entretenir très soigneusement.
Un distributeur tous les 20 kilomètres
Le centre de formation conserve ses postes à souder les plus anciens. Ceux-ci n'étaient pas encore "intelligents", mais ils étaient suffisants pour réparer des véhicules fabriqués avec des tôles plus épaisses, dans des aciers plus simples qu'aujourd'hui. ©J2R/NG
Pour commercialiser l'ensemble de son catalogue, le groupe mise sur un réseau de distributeurs premium. Celui-ci inclut les principaux groupements de distributeurs d'équipements de réparation automobile. Il diffuse ainsi ses produits, avec une exigence de haute qualité de service. Celle-ci inclut le prêt d’équipements et la fourniture de consommables. Aussi, la société sélectionne minutieusement ses partenaires pour assurer un service optimal. Elle n’hésite pas à rompre avec ceux qui ne respectent pas ses critères de qualité.
Parallèlement, la proximité est l'un de ses piliers fondamentaux. Ainsi, en France, Gys essaie d'entretenir un réseau de distributeurs tous les 20 kilomètres. Elle les soutient via son propre service après-vente. Celui-ci s'étend dans ses filiales. Dernièrement, ceux d'Allemagne et d'Espagne ont bénéficié d'importants investissements. Ces implantations à l'international sont un autre point clef de la stratégie du groupe pour maintenir son avance technologique.
Suivre les évolutions automobiles
"Avant dans l'automobile on regardait les États-Unis. Plus tard, les regards se sont braqués sur l'Allemagne, puis le Japon. Aujourd'hui, il faut surveiller la Chine et l'Inde, tout en regardant les innovations aux États-Unis. Nous entrons dans un cycle où l'on innove dans plusieurs régions du monde en même temps", affirme Bruno Bouygues. Son implantation lui permet d'assurer cette veille pour s'adapter aux méthodes de réparation des véhicules les plus récents – y compris ceux produits en gigacasting.
À lire aussi : Gys simplifie la soudure de goujons avec le Capatek 66 FV
Le groupe entretient ainsi une proximité de plus en plus importante avec tous les constructeurs automobiles, pour leur fournir de l'équipement. Ce partenariat technologique est longtemps resté confiné à l'après-vente. Il concerne maintenant aussi la production, avec des technologies robotisées. Ainsi, Bruno Bouygues affirme que "cela fait longtemps que nous sommes connus mais nous commençons tout juste à être reconnus. Nous recevons maintenant de plus en plus d'appels entrants des marques".