Peinture : Impressions croisées
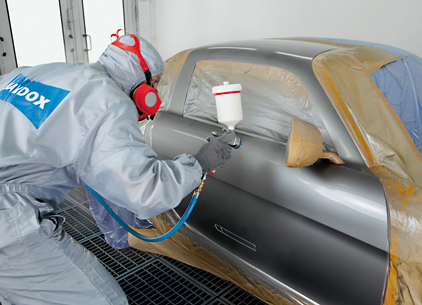
Les fabricants de peintures tentent de coller au plus près des nouvelles tendances, quand ils ne les précèdent pas. Avec en toile de fond, les mêmes impératifs… Toujours… Comment intégrer les nouvelles formules, tout en améliorant la rentabilité du poste peinture pour circonscrire les baisses du volume d’activités dans la réparation collision.
L’un des premiers artifices fut la mise en place de structures de “spot repair”, capables de traiter rapidement les petits travaux, pour un temps d’immobilisation minimum de la voiture. Nombre de produits furent alors développés spécifiquement pour ces applications, les vernis UV notamment. Mais d’autres pièges se mettent d’ores et déjà en travers de la route des peintres, les finitions mates et les peintures tri-couches à effets notamment.
Mats : un contretypage délicat
“La finition mate est un phénomène de mode, signale Jean Papachryssanthou, responsable technique EMEA d’Akzo Nobel. L’essentiel est de réussir à contretyper les aspects finis.” Les fabricants utilisaient jusque-là des bases à mater qui étaient mélangées à un vernis brillant, avec la difficulté de composer la bonne proportion et de réaliser un mélange homogène. “Nous utilisons deux vernis spécifiques, un satiné et un mat, précise Jean Papachryssanthou. Le résultat est obtenu en utilisant les deux produits dans des proportions pré-adaptées aux teintes utilisées par les constructeurs.”
Chez DuPont Refinish, Jean-Marc Sauvaget le directeur technique, propose : “Pour réaliser le bon mélange, le réparateur se connecte à la base informatisée ColorNet-Pro, qui fournit au peintre les proportions à respecter pour obtenir le rendu d’origine.” DuPont utilise un glossmètre pour déterminer les proportions de produits nécessaires à l’obtention du bon niveau de brillance… ou de matité. Cet appareil mesure la réflexion de la lumière sous un angle de 60°. La difficulté est d’obtenir le niveau de mat respectant les choix des constructeurs. Le “glossmètre” qui évalue le niveau de mat d’un vernis est néanmoins coûteux pour un atelier de réparation, en raison de l’usage qui peut en être fait. Il est préférable d’utiliser des échantillons étalonnés qui permettent de reproduire le niveau de mat correct. Chez PPG, qui revendique une connaissance historique sur la peinture mate, ayant importé sa technologie avec les véhicules militaires américains dans les années 40, Frédéric Pflanz, responsable technique couleurs et formation, précise “la principale solution à la réussite d’une finition mate est une bonne formation.”
La nécessaire formation
Thierry Leclerc, responsable technique et marketing France de BASF Coatings, compare la complexité des finitions mates à celle des teintes à effets, désormais très répandues chez les constructeurs. “Pour Glasurit, notre approche conduisant à la réalisation de mats, prend la forme d’un stage nommé “ratio VOC experts, spécial finitions à effets”, qui va traiter les vernis mats, et également des coloris extrêmement difficiles à réparer, comme les tri-couches, le “rouge flamme” de la Renault Clio par exemple”, détaille-t-il.
Auparavant, le peintre gérait sa couleur grâce à la couche de base. Selon la technologie tri-couche, c’est la combinaison des deux couches (base et premier vernis) et leur épaisseur, qui restitue la couleur définitive. C’est donc beaucoup plus technique. Concrètement, un vernis coloré vient recouvrir la couche de base, puis une seconde couche de vernis transparent vient parfaire la finition. C’est une technique qui donne plus de profondeur et des effets. Le vernis intermédiaire est brillant ou mat, selon les fabricants.
Les solutions “UV” peinent à convaincre
Autre sujet de réflexion pour les fabricants, les produits qui sèchent aux ultra-violets, ne font pas l’unanimité. Ainsi, DuPont Refinish, par la voix de son directeur technique, n’en voit pas une utilisation massive. “Il faut savoir que cela reste un axe de recherche pour l’avenir”, nous dit Jean-Marc Sauvaget. Le groupe a présenté ce type de produit il y a déjà 20 ans, il avait à l’époque été récompensé d’un Grand Prix de l’Innovation à Equip Auto. Mais le coût d’un équipement complet dans une cabine pour utiliser des produits séchés aux UV est trop important pour être appliqué autrement que sur de petites réparations. Deux techniques de séchage existent : les UV “A” et UV “B”. Les “UV A” permettent de sécher en 2 à 3 minutes. Celles fonctionnant aux “UV B” sèchent dès lors qu’elles sont exposées à un “flash” d’ultraviolets “B”. Une exposition de 30 secondes est alors suffisante. Compte tenu de la difficulté d’usage, on ne va réaliser ce type de réparation que sur des surfaces réduites de la taille d’une feuille A4. De plus, les “UV B” sont dangereux pour la santé et exigent des précautions d’usage.
Chez BASF, on est encore en phase d’apprentissage sur ces produits : “Il y a trop d’avantages économiques pour qu’on n’y aille pas, note Thierry Leclerc. Il faut que la technique soit accompagnée d’un équipement qui ne soit pas une usine à gaz. C’est une technique qui s’accorde bien avec l’état actuel de la réparation, qui fait de moins en moins de peintures complètes. La petite réparation est parfaitement adaptée aux UV, pour des boucliers par exemple, qu’il ne faut pas trop chauffer et que l’on réalisera sur l’aire de préparation.”
Les solutions de la réparation rapide
Opinion différente chez Lechler : “Pour répondre aux besoins du spot repair, il est plus intéressant de proposer des produits plus efficaces, préfère Marta Radice, responsable marketing de Lechler pour la France. Les produits à séchage ultraviolet nécessitent un investissement trop important.” Chez R-M / Glasurit on admet également que “les produits UV ne seront pas des remplacements, mais des compléments de gammes et des produits en plus.”
L’ensemble des fabricants cherche à réduire les temps de process. “BASF va lancer des sous-couches qui pourront s’appliquer directement sur le métal, révèle Thierry Leclerc. Ces sous-couches seront couvrables sans ponçage. L’objectif est de gagner encore du temps sur l’ensemble de la réparation. Pas de primaire, pas de séchage, pas de ponçage ; on ne peut pas faire plus court.” Frédéric Pflanz, chez PPG fait le même constat : “Il faut produire plus avec moins de temps. Nous avons des vernis rapides, qui nécessitent moins de préparation et moins de couches.”
Travailler les méthodes
Notre interlocuteur chez PPG le met en avant : “Pour répondre à une meilleure rentabilité du poste peinture, il faut un produit qui répond exactement aux besoins du réparateur, mais il faut surtout respecter ses méthodes d’utilisation. Il n’y a plus de mauvais produits, mais des produits mal utilisés.” Une seule solution selon les fabricants, pour répondre à ce diagnostic, la formation. “Il faut, de plus en plus, faire du sur-mesure”, selon Frédéric Pflanz. Malheureusement, les peintres sont difficiles à déplacer. “Ce sont les peintres qui viennent en formation, mais ce sont les responsables d’atelier qu’il faut convaincre, déplore Thierry Leclerc chez BASF. Quand le peintre est absent pendant 2 jours dans une petite structure, les voitures ne sortent plus. Nous avons compté que nous les voyons 2 jours tous les 14 ans, alors qu’il faudrait qu’ils viennent tous les 4 à 5 ans au centre de formation de Clermont de l’Oise.”