Les nouveaux turbocompresseurs
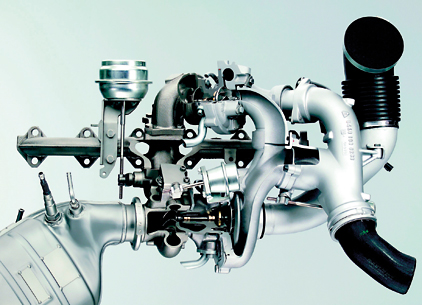
Le turbocompresseur est désormais reconnu comme indispensable à l’amélioration des performances, y compris pour répondre au downsizing et aux normes de pollution. Cet équipement, qui a longtemps été synonyme de puissance pour les moteurs à essence, s’est adapté au marché et de nombreux fabricants sont désormais en concurrence.
Bosch, Continental, sont venus rejoindre les fabricants historiques de turbocompresseurs Honeywell (Garrett), Borg Warner (ex-KKK), IHI, Holset, Mitsubishi. Le marché, qui s’est limité jusqu’à présent aux moteurs Diesel et à quelques modèles sportifs, est aujourd’hui dopé par le downsizing, qui équipe des mécaniques de 600 à 1 400 cm3 d’un turbocompresseur augmentant la puissance et le couple jusqu’à 50 %. Mais les défauts des turbocompresseurs sont toujours présents et pour les surmonter, de nombreuses techniques sont utilisées.
Les nouvelles solutions des turbocompresseurs
Pour diminuer le temps de réponse de la turbine, le premier moyen est de limiter l’inertie du rotor. Soit le dessin évolue, soit la dimension du compresseur décroît. Cette évolution prend désormais de multiples formes qui ajoutent encore plus de performances à la turbine. Une seconde solution consiste à additionner les turbines les unes après les autres, c’est la solution “twin turbo” voire à trois turbocompresseurs. Enfin, pour limiter le temps de latence de la mise en pression du circuit, la solution turbine à entraînement électrique ou compresseur volumétrique en série avec le turbocompresseur est également adoptée par les constructeurs. Toutes ces solutions recherchent le même résultat, optimiser le rendement et l’utilisation de l’énergie perdue dans les gaz d’échappement.
Twin turbo
Tous les constructeurs n’utilisent pas la mise en série des turbocompresseurs, mais pour ce qui est de la grande série, on en trouve chez PSA Peugeot Citroën, Opel, BMW. La solution consiste à additionner un turbocompresseur de faible dimension à un gros compresseur. Ils peuvent travailler en série comme en parallèle, avec un bypass sur une des suralimentations.
Un petit turbocompresseur, ou turbo basse pression, est continuellement en fonction. Léger, il est actif même à bas régime, avec des débits de gaz d’échappement réduits. Il assure une suralimentation légère qui permet un fonctionnement normal du moteur, même avec un taux de compression réduit. Lorsque le régime et la charge moteur atteignent les limites de suralimentation du premier compresseur, un second turbocompresseur entre en action. Plus gros, il autorise des débits d’air plus importants, mais il est moins rapide à entrer en action et entraîne un délai de réponse par rapport à l’action sur l’accélérateur. Pour alimenter avec un volume de gaz plus important le gros turbo, un clapet de dérivation du premier compresseur peut être installé sur le collecteur d’échappement. De la même manière, une dérivation peut accélérer le passage des gaz du gros turbo jusqu’à la tubulure d’admission sans passer par l’étranglement que constitue le petit turbocompresseur.
Sur un modèle récent à 6 cylindres, BMW a installé ainsi trois turbocompresseurs dont deux assurent le premier niveau (un turbo pour trois cylindres) et le second de grosse dimension est actif à haut régime pour les fortes suralimentations.
Turbocompresseur et compresseur volumétrique ou électrique
Pour obtenir une suralimentation active dès les bas régimes, l’idéal est d’utiliser un compresseur volumétrique. Le débit d’air est exactement proportionnel au régime. Ce mode d’entraînement du compresseur est très consommateur d’énergie puisqu’il est entraîné depuis le vilebrequin. L’installation d’un compresseur de petite dimension, éventuellement débrayable, permet, sans perte de rendement important, d’obtenir une première phase de suralimentation. La même solution est désormais obtenue avec l’utilisation d’un compresseur à motorisation électrique, une solution adoptée par Audi sur son dernier V6 TDI de 3,0 l qui développe plus de 100 ch au litre (326 ch).
Les perfectionnements des turbocompresseurs
Pour assurer un meilleur écoulement des gaz dans la turbine du compresseur, les constructeurs ont adopté une solution assez simple et statique, la double entrée sur la turbine motrice, ou “Twin Scroll”. Le rendement est amélioré par diminution de la contre-pression que la présence du turbocompresseur génère par un freinage des gaz. Cette technique est une alternative aux turbocompresseurs à géométrie variable (TGV ou VNT).
Pour obtenir de meilleurs résultats, Honeywell termine la mise au point d’un nouveau type de turbocompresseur, plus léger, plus rapide et capable de délivrer un volume d’air plus important. La solution consiste à placer deux turbines en parallèle sur l’axe du système classique. Celles-ci sont d’un diamètre moins grand et laissent un passage moindre à l’air, mais elles sont deux, ce qui double le volume d’air compressé.
Avec l’évolution des modes de circulation, avec des trajets toujours plus courts et des vitesses moindres, les techniciens attendent des turbocompresseurs qu’ils réduisent les pertes par frottement. L’adoption de roulements à la place de paliers lubrifiés améliore la réponse du turbo, d’environ 25 % jusqu’à 2 000 tours minutes pour un moteur 2,0 l. Les roulements opposent une résistance moindre, sont moins sensibles à la température et à la qualité de l’huile.
La compétition
La Formule 1 utilise depuis cette saison des moteurs turbocompressés où un seul turbo alimente les deux rangées de cylindres (V6 de 1,6 l). Pour limiter le délai de réponse de ce turbo délivrant une pression importante, un générateur-moteur électrique est placé sur l’axe, et permet à la fois une récupération d’énergie lors des décélérations et une relance de la turbine simultanée à la phase d’accélération.