L’air comprimé dans l’atelier
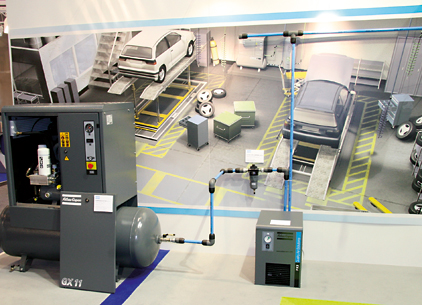
L’air comprimé constitue la source principale d’énergie de l’atelier. Souple d’usage et bon marché, cette énergie convient à de nombreuses applications, que ce soit pour l’outillage à main, le gros équipement de l’atelier ou le travail de la carrosserie, sans oublier que l’air comprimé est indispensable au gonflage des roues, au nettoyage des pièces ou au séchage de la peinture en carrosserie. Mais des pièges peuvent transformer ces atouts en gouffre énergétique.
Le compresseur
Deux types de compresseurs sont utilisés en réparation automobile, les compresseurs à piston et les compresseurs à vis. Le choix du compresseur doit se faire en rapport à l’activité de l’atelier et au volume d’air utilisé.
Le compresseur à vis, d’une conception plus récente, est plus économique à l’usage, mais plus coûteux à l’acquisition. Ce type de compresseur présente l’avantage de fonctionner à une température assez basse (35 °C) mais, de ce fait, il condense dans son carter quand il ne tourne pas. Il est donc indispensable que le compresseur à vis tourne au moins 60 % du temps. Au contraire, le compresseur à piston ne doit pas dépasser 60 % de son temps en fonctionnement et, en fonctionnement normal, doit être arrêté au moins 50 % du temps.
Anest Iwata, qui lance une gamme de compresseurs, propose un compresseur à vis à vitesse variable. En fonction du besoin en air comprimé, le moteur d’entraînement du compresseur tournera plus ou moins rapidement. Une gestion électronique régule la vitesse de rotation.
Le compresseur à piston est souvent à deux étages, un premier piston (basse pression) comprimant l’air à un premier niveau de pression (environ 4 bars). L’air est ensuite refroidi pour en augmenter la densité et passe dans un second cylindre où il parvient à sa pression définitive de 10 à 14 bars. Le premier cylindre est de plus grand diamètre que le second pour compenser le volume supérieur de l’air à pression atmosphérique. Le compresseur à double étage augmente le rendement, réduit les contraintes mécaniques et permet d’amener la pression finale jusqu’à 14 bars.
Pour résumer, quand le compresseur à piston aspire 100 litres d’air, il produit 70 litres d’air comprimé, et présente donc un débit réel de 42 litres en respectant un repos de 40 % du temps. Le compresseur à vis aspire 100 litres, il produit 100 litres d’air comprimé, et présente donc un débit réel de 100 litres sans arrêt de fonctionnement.
L’alimentation électrique des compresseurs est souvent sur le réseau 400 V (triphasé). Le moteur peut être câblé en direct ou en triangle. Cette dernière solution limite les appels importants d’intensité au démarrage du moteur. L’intensité de démarrage est trois fois plus importante que l’intensité nominale de fonctionnement en mode de branchement “étoile” alors qu’elle est six fois plus importante en mode direct. Une consommation de 22,8 ampères sur un moteur de 4 kW demandera 45,6 ampères en branchement direct. (source Provac)
Les cuves
Le volume est généralement associé à la puissance du compresseur.
Fabricant de compresseurs, Guernet apporte ses préconisations. “Pour un garage avec deux mécaniciens, il faut un compresseur de 5,5 chevaux et une cuve de 300 à 500 litres, précise Marie Xavier, responsable communication et ventes. Au-dessus, on préconise pour une puissance de 10 à 15 chevaux une cuve de 500 litres. On passe à 1 000 litres pour une puissance de 15 chevaux si c’est nécessaire, et on est systématiquement à cette capacité pour 20 chevaux. Cet équipement est utilisé pour des carrosseries et de gros négociants de pneumatiques, surtout ceux qui font du poids lourd, pour lequel les besoins d’air sont très importants. Pour un gros MRA, une agence de marque, le montage traditionnel reste de 7,5 chevaux avec 10 bars de pression. Le compresseur de 10 chevaux sera utilisé pour une concession, mais toujours en technologie piston, moins coûteuse à l’acquisition que le compresseur à vis, et qui s’impose par un usage moins constant qu’en carrosserie. Le compresseur à piston tourne en moyenne 40 % du temps, le compresseur à vis tourne entre 60 et 100 % du temps. Si le compresseur à vis ne tourne pas assez, il condense et risque une rupture mécanique par accumulation d’eau dans le carter. On retrouvera donc le compresseur à vis en carrosserie ainsi que chez les spécialistes pneumaticiens, qu’ils soient VL ou PL. Les centres-autos ont un volume d’activité très important avec de nombreuses baies qui font beaucoup de montage de pneumatiques. Chez eux, le compresseur peut tourner jusqu’à 2 500 heures par an, et on adopte alors une technologie à vis.”
L’épuration de l’air
Il faut épurer l’air de plusieurs manières. Un filtre mécanique anti-poussières stoppe les particules jusqu’à 0,1 micron. Dans tous les montages, nous préconisons l’équipement d’un sécheur d’air. Celui-ci élimine la vapeur d’eau présente dans l’air comprimé qui a tendance à condenser. Cette protection est indispensable pour les appareils pneumatiques. Nécessaire également sur les compresseurs à vis, en amont du compresseur. Ce dernier fonctionne à température à peu près constante (environ 35 °C) et condense plus. Le principe de fonctionnement est une baisse de la température de l’air comprimé (à 3 °C environ), l’humidité présente se condense et est évacuée par une purge automatique. Pour la peinture, on installe des filtres “microfiltre” à 0,1 micron.
Séchage de l’air comprimé
En raison de la compression de l’air, la part d’eau en vapeur dans l’atmosphère va tendre à se condenser dès le retour à une température normale. Pour limiter le passage de cette eau dans le réseau de l’atelier avec le risque de dommages sur les appareils, entre le compresseur et le réservoir, les fabricants préconisent l’installation d’un sécheur d’air. Il consiste en un refroidisseur qui conduit à la condensation de l’eau. Celle-ci est extraite par un purgeur automatique.
Blocs filtration-lubrificateur
Pour obtenir la qualité d’air optimale sur chaque poste, avant le connecteur de branchement, il est possible d’installer sur le réseau des blocs filtre-régulateur-lubrificateur ou un bloc de filtration-régulation pour l’application de peinture. Ces éléments sont fournis comme ensembles, permettant de limiter la perte de charge. Le régulateur peut par ailleurs limiter la pression pour disposer d’une pression parfaite pour les outils utilisés, tout en proposant un réseau beaucoup plus puissant pour des usages comme le service au pneumatique. Le lubrificateur permet d’introduire des vapeurs d’huile pour les appareils mécaniques qui nécessitent un graissage afin de favoriser leur durée de vie (Pistolet à chocs, burins, cliquets pneumatiques…).
Le réseau
Le réseau d’air comprimé de l’atelier peut être réalisé avec quatre technologies distinctes. Le montage traditionnel est fait de gros tubes d’acier soudés. Coûteux à réaliser (beaucoup de main-d’œuvre), peu adaptable (les modifications nécessitent de gros travaux), le réseau en acier est également la proie de la corrosion et l’état de surface brut des tubes entraîne des chutes de pression en ligne (perte de charge) inutiles. Pour une utilisation sur un réseau nécessitant une absolue propreté et peu exigeant en modifications, l’acier peut être remplacé par de l’inox. Pour les ateliers de mécanique automobile et les carrosseries, deux solutions sont privilégiées : le tube d’aluminium et le PVC. Les deux techniques se présentent en “préfabriqué” avec des raccords vissés, sertis ou collés (pour le PVC). En respectant des règles de montage simples qui sont préconisées par chaque fabricant, il est possible de réaliser soi-même et très rapidement un réseau performant. Disponibles en 3 à 6 mètres de longueur, les tubes sont d’un diamètre de 20 à 80 mm. Pour un atelier automobile, on privilégiera les diamètres de 20 à 40 mm maxi. De nombreux accessoires permettent de concevoir le meilleur circuit possible, dont il est recommandé qu’il soit en circuit fermé, pour assurer une perte de charge minimale. Sur le circuit, il sera installé des éléments de compensation de dilatation ainsi que des amortisseurs de surpression qui absorberont les irrégularités de mise en pression par le compresseur. PVC et aluminium présentent l’avantage d’une tenue parfaite au vieillissement. L’aluminium est moins sensible et générateur de condensation, il est presque totalement démontable, mais son coût est supérieur (environ 20 %) à un montage PVC ou acier soudé.
Les conseils
Sécurité, normes et obligations Le circuit d’air comprimé ne fait pas l’objet d’une quelconque réglementation, c’est le réservoir qui doit obéir à des normes et des contrôles. Plusieurs règles sont à suivre suivant le volume et la pression maxi des équipements, d’une part pour le contrôle en fabrication (avant installation), d’autre part en contrôle périodique de sécurité.
En fabrication, les équipementiers sont tenus à respecter des directives européennes, la 87/404/CEE pour les réservoirs d’une pression maximale inférieure ou égale à 30 bars, et d’un rapport pression/volume inférieur à 10 000 bars/litre. Le second règlement (directive 97/23/CE) est appliqué aux réservoirs non concernés par la première norme.
Selon le cas, les réservoirs auront un marquage “CE” suivi du numéro de l’organisme de contrôle. La plaque comporte alors la pression maximale de service (PS, en bars), la température maximale de service (T max en °C), la température minimale de service (T min en °C), la capacité du réservoir (V en l), le nom et marquage du fabricant, le type et l’identification de série ou du lot du réservoir, les deux derniers chiffres de l’année d’apposition du marquage “CE”. Pour les plus gros réservoirs, le marquage comporte : la capacité du réservoir (V en l), la pression d’essai PT appliquée (pression relative en bars) et la date, la pression et le tarage de la soupape à la pression de service, le groupe de gaz admissibles (pour air et azote, il s’agit du groupe 2).
En application de l’arrêté du 15 mars 2000, le contrôle est soumis à trois règles. Pour un rapport Pression (PS)/volume inférieur ou égal à 200 bars/litres, l’utilisateur n’est pas soumis à un contrôle. Il s’agit de réservoirs d’utilisation privée. Pour les réservoirs d’un rapport pression (PS)/volume inférieur à 10 000 bars/litres, la déclaration de mise en service n’est pas obligatoire, elle l’est pour les réservoirs supérieurs à ces caractéristiques. Pour tous, les prescriptions figurant à l’arrêté du 15 mars 2000 sont à respecter, une visite périodique (visuelle) est à faire tous les quarante mois et une épreuve sous pression (épreuve hydraulique) est à effectuer en complément tous les dix ans.
----------
Les conseils d’un fabricant
Les circuits d’air comprimé des ateliers nécessitent une attention particulière ? “Oui, on s’aperçoit lors des visites dans les ateliers que beaucoup de compresseurs fonctionnent à 100 % de leur capacité, c’est-à-dire en permanence pour compenser les fuites présentes sur le circuit. Les fabricants, dont Guernet, font à la demande des audits pour sensibiliser les responsables à l’entretien, la réparation des installations et le renouvellement des systèmes. Les compresseurs à pistons qui tournent en permanence ne sont pas faits pour cela, le risque est d’avoir des pannes.
Les techniques de réseaux disponibles actuellement permettent de réaliser des circuits fiables et avec des pertes de pression en ligne moindre. Les vieux circuits sont du domaine de la plomberie, les tubes en acier soudés génèrent de la rouille et de l’humidité qui circulent dans le circuit en endommageant les appareils.
On rencontre plusieurs types d’installations pour remplacer cette technique, le PVC collé, l’aluminium et l’inox serti. Le réseau en PVC collé condense peu, et les poussières sont peu présentes dans ces circuits qui peuvent rester propres longtemps. Néanmoins, toute modification du réseau conduit à des travaux compliqués. Pour des réseaux plus performants, on préférera l’aluminium. Ce type d’équipement est propre, entraîne des pertes de charge minimum et génère peu de condensation.
En tête d’affiche, l’inox est garant d’une corrosion très réduite dans le temps. Comme pour l’aluminium, le montage est serti. Le coût est proche de celui du montage en tubes d’aluminium, et supérieur de 20 % environ à celui du PVC.
Les conceptions actuelles sont orientées vers un circuit fermé. Il est également possible d’installer un second réservoir en bout de ligne. Il faut dans tous les cas réduire au minimum les pertes de charge en supprimant les coudes, utiliser des descentes avec la même qualité de matériau et diamètre que sur le circuit principal. La perte de charge est difficile à quantifier. Il existe des abaques théoriques donnant des indications aux installateurs. Par exemple, pour 30 m, pour un débit de 70 m3 à l’heure à 6 bars, il y aura une perte maxi admissible de 5 %. Si on veut descendre à 0,1 bar de perte, il faut augmenter le diamètre du tuyau. Ceux-ci sont proposés en 4 diamètres : 16 mm, 25 mm, 40 et 63 mm. Le dernier est utilisé en industrie, le 40 mm est recommandé pour les ateliers poids lourds. Pour être performant et par précaution, on monte du diamètre 25 mm sur tout le circuit. Il est raisonnable d’utiliser le même diamètre partout, soit 25 mm. Le coût ressort quasi identique.”