Le modèle vertueux des alternateurs remanufacturés
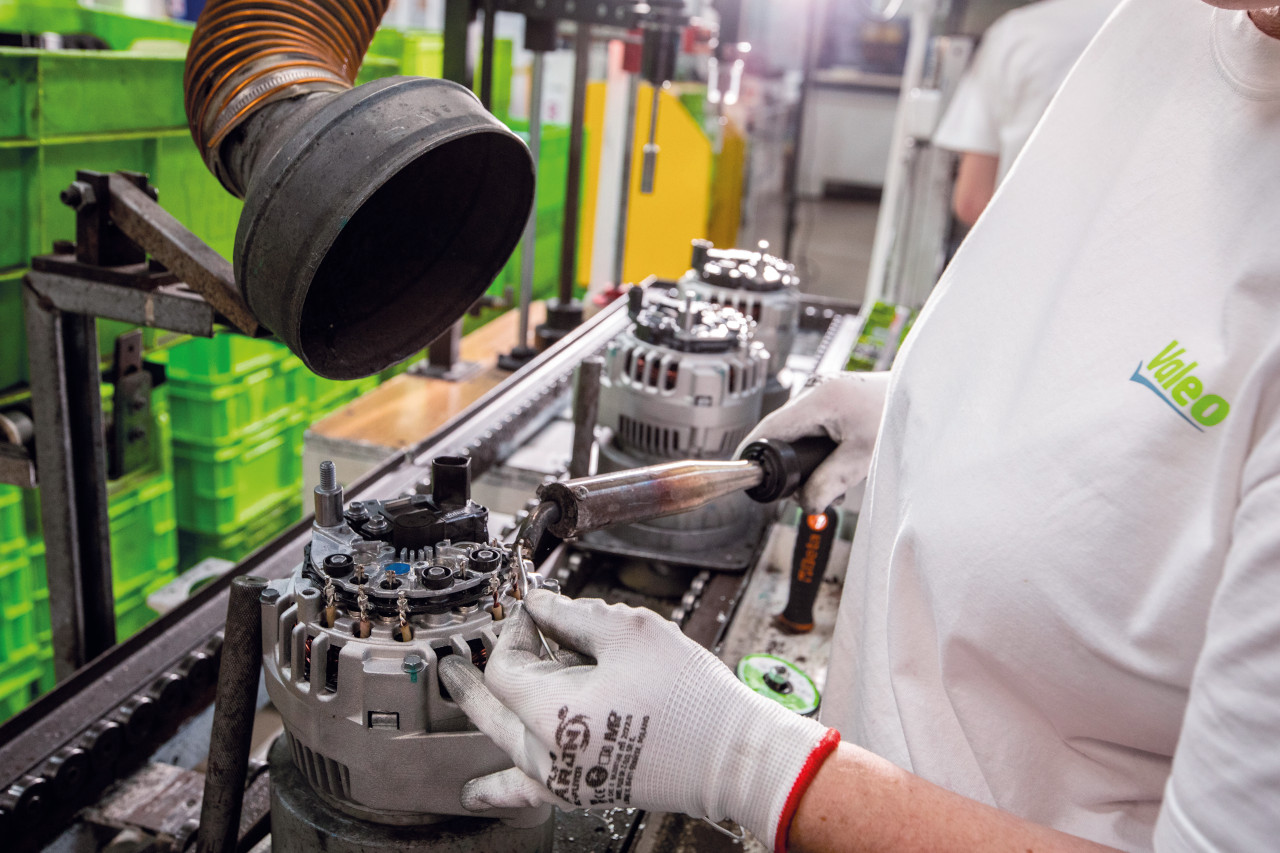
Famille iconique du remanufacturing des pièces détachées automobiles, l'alternateur représente aussi un véritable enjeu pour le développement de l'économie circulaire à la rechange. Chaque pièce dispose d'environ 5 kg d'acier, de cuivre, d'aluminium et d'électronique à sauver.
Grâce au savoir-faire acquis au long des années, la remanufacture permet d'offrir une deuxième vie à ces produits, avec une qualité identique à la pièce d'origine pour un coût moindre et un bien meilleur bilan environnemental.
L'échange standard, une solution vertueuse
Généralement, le terme "échange standard" est utilisé pour qualifier le cercle vertueux de collecte et de remanufacture d'une pièce usagée : l'utilisateur reçoit un produit remanufacturé aussi performant qu'un produit neuf et il retourne "en échange" son produit défectueux. La remanufacture offre trois principaux intérêts :
- Le premier est de réduire l'impact environnemental. Un alternateur remanufacturé permet de réutiliser jusqu'à 90 % du poids des composants.
- Autre avantage : le rapport qualité-prix. Un produit remanufacturé dans un modèle d'échange standard est idéal pour les professionnels à la recherche d'une solution économique, en moyenne 30 % moins chère qu'un produit d'origine neuf.
- Sur des modèles de véhicules plus anciens, certains composants ne sont plus disponibles, car ils ne sont plus produits par le fournisseur d'origine. Il devient alors difficile de trouver un produit de remplacement strictement identique.
De la collecte de vieille matière au contrôle final
La gestion des carcasses, une étape essentielle de l'échange standard. "Pas de carcasse, pas de remanufacture" : il s'agit d'un principe fondamental dans le processus de l'échange standard. Une bonne gestion du retour des carcasses est donc une nécessité absolue pour une remanufacture de qualité. À leur arrivée sur le site du remanufacturier, une attention particulière est mise sur le tri, l'évaluation de la qualité et le stockage de chaque produit.
Plusieurs dizaines de tests sont menés tout au long des étapes de la rénovation des alternateurs pour garantir la qualité et la longévité des produits. ©Valeo
Même si la logistique de retour peut parfois paraître complexe, la plupart des acteurs majeurs de ce marché en Europe ont mis en place des outils et des processus pour la simplifier. Valeo, par exemple, dispose de son propre logiciel de gestion et va même jusqu'à identifier chaque carcasse avec une étiquette unique pour une traçabilité complète.
Cette étape est essentielle, car chaque référence d'alternateur possède sa propre nomenclature, avec des composants et des caractéristiques spécifiques nécessitant un processus de remanufacture et de contrôle adapté.
Le démontage
C'est la première étape du processus industriel. Les carcasses sont traitées par lots homogènes contenant plusieurs carcasses d'une même référence. Il s'agit là d'une différence majeure entre des alternateurs remanufacturés et des alternateurs réparés. Dans la réparation, chaque pièce est d'abord diagnostiquée pour déterminer les actions à effectuer. En général, la réparation est réalisée pièce par pièce pour traiter uniquement le ou les défauts identifiés.
Pour les produits remanufacturés, toutes les carcasses sont démontées et détaillées en composants. Ceux-ci sont regroupés par type : les rotors, les stators, les paliers, les régulateurs, les ponts… jusqu'à certaines visseries ! L'évaluation de la qualité est effectuée individuellement pour chaque composant, permettant de certifier des performances équivalentes au produit d'origine.
Le nettoyage
Le nettoyage est indispensable pour avoir des composants propres permettant une première évaluation de qualité précise, et pour l'aspect visuel du produit final. Les opérations de nettoyage sont adaptées à chaque composant pour éliminer les différents types de résidus : graisse, huile, rouille, etc. Cette étape est obligatoire pour rendre un aspect plus attrayant à certains éléments, tels que les paliers.
Différents équipements et agents de nettoyage peuvent être utilisés : lavage en machine, grenaillage ou nettoyage par ultrasons. Ces processus sont optimisés pour générer une consommation d'eau et d'électricité moindre, s'inscrivant dans des systèmes de gestion durable avec des équipements à circuit d'eau fermé.
La remanufacture de sous-ensembles
Cette étape est au cœur de la remanufacture. Pour l'illustrer, voici deux exemples :
- Les rotors : L'opération consiste à contrôler la fonctionnalité électrique. Certains acteurs de la filière vont jusqu'à restaurer la durabilité du produit, par exemple avec le regarnissage des bagues collectrices, considérées comme la principale cause d'usure.
- Les ponts redresseurs : ces éléments assurent le passage du courant alternatif à un courant continu. Il s'agit ici d'identifier la ou les diodes défectueuses afin de remplacer tout ou partie du pont.
Le remplacement de certains composants
Les composants sujets à usure et qui ne peuvent pas être remanufacturés sont systématiquement remplacés par des composants neufs. Par exemple les roulements, certaines visseries…
L'assemblage et contrôle final
Il s'agit de la dernière étape. Tous les composants et sous-ensembles validés au cours du processus sont envoyés sur une ligne d'assemblage. Cette opération s'articule autour de plusieurs interventions :
- Montage des roulements.
- Centrage du stator dans le palier.
- Compactage.
- Montage de la poulie.
- Opérations de serrage avec contrôle du couple et de l'angle de serrage.
- Soudure des phases du stator avec le pont redresseur.
- Montage du capot arrière.
- Tests de fin de ligne pour s'assurer du fonctionnement de chaque produit remanufacturé.
Puis la carcasse prend un nouveau départ…
Après réparation du véhicule à l'aide d'un produit rénové, l'alternateur défectueux devient la matière première d'une prochaine remanufacture. Il est donc essentiel de la retourner au fournisseur pour un prochain besoin. Ce retour de la carcasse garantit la circularité de l'échange standard, où chaque pièce trouve une seconde vie avec un minimum de nouvelles ressources et une contribution à la réduction des déchets.