Maxime Richaud, Autocirc : "2025 sera une année charnière pour le réemploi"
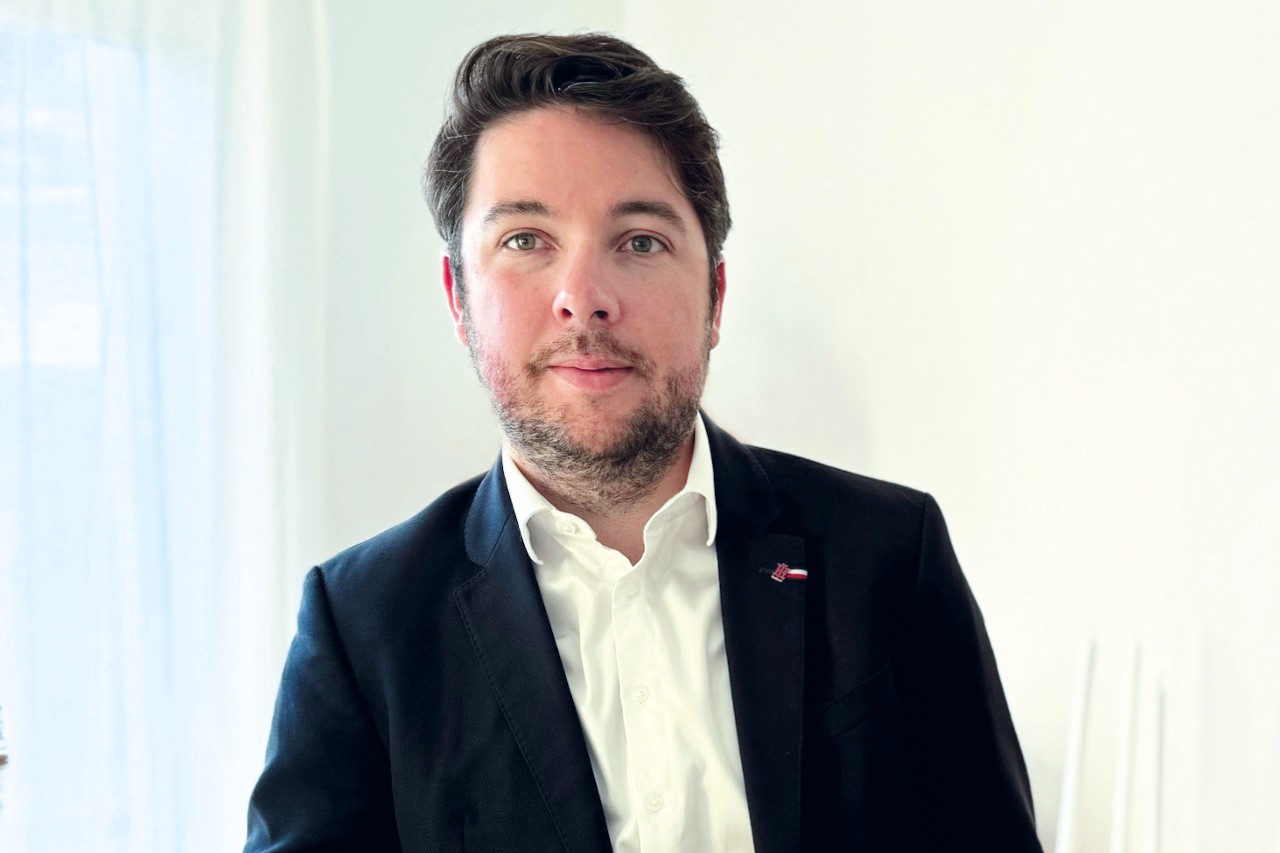
Le Journal de la Rechange et de la Réparation : Présentez-nous tout d’abord le groupe Autocirc…
Maxime Richaud : Le groupe Autocirc a été fondé entre 2019 et 2020 en Suède par Johan Livered et Mattias Pettersson, deux recycleurs automobiles. Leur idée était de créer un écosystème complet, dédié à l’économie circulaire dans le secteur automobile. Le nom "Autocirc" illustre parfaitement cette ambition : "auto" pour automobile, et "circ" pour circularité. Leur objectif était d’englober toutes les étapes nécessaires pour valoriser les ressources issues des véhicules, depuis leur fin de vie jusqu’à leur réintroduction sur le marché.
Aujourd’hui, le groupe Autocirc regroupe 66 sociétés implantées dans plusieurs pays européens et emploie 1 260 collaborateurs. Le recyclage automobile est notre cœur de métier, mais il est intégré dans une vision plus large qui englobe également le transport, le remanufacturing et la distribution de pièces de réemploi. Nous nous sommes donné pour mission d’offrir des solutions durables, en ligne avec les objectifs de réduction des déchets et de limitation de l’impact environnemental.
J2R : Comment se structure l’approvisionnement des véhicules dans vos centres de recyclage ?
M. R. : Nous avons deux principaux gisements pour alimenter nos centres. Le premier, historiquement utilisé dans le secteur du recyclage, est constitué par les véhicules en fin de vie. Ce sont des voitures souvent âgées, qui ont atteint le bout de leur cycle d’utilisation et que leurs propriétaires souhaitent céder. Ces véhicules nous sont soit directement apportés par des particuliers, soit collectés chez eux. Rappelons qu’en France, la réglementation oblige les centres de recyclage à accepter ces véhicules gratuitement lorsqu’ils sont déposés. Cette mission de service public est indispensable pour assurer une gestion responsable des véhicules hors d’usage.
Cependant, ces véhicules en fin de vie ne constituent pas notre ressource principale, parce qu’ils contiennent des pièces usées ou obsolètes, ce qui limite leur potentiel de réemploi. C’est pourquoi nous nous tournons majoritairement vers notre second gisement : les véhicules issus des compagnies d’assurance. Ils sont bien plus intéressants pour nous, car ils étaient en état de circuler avant leur sinistre. Leurs composants sont donc souvent en bon état. Plus de 95 % des véhicules que nous traitons proviennent de ce gisement, qui représente une ressource stratégique pour notre activité.
J2R : Pouvez-vous détailler les étapes de traitement des véhicules dans vos centres ?
M. R. : Lorsqu’un véhicule arrive dans l’un de nos centres, il passe par une série d’étapes bien définies. La première est la dépollution, qui consiste à retirer tous les fluides et matériaux dangereux ou polluants (huiles, carburants, batteries…). Cette étape est essentielle pour garantir un traitement respectueux de l’environnement. Ensuite, nous procédons au démontage des pièces réutilisables. Certaines, comme les moteurs, les alternateurs ou les éléments de carrosserie, peuvent être revendues immédiatement après contrôle.
D’autres nécessitent un travail de remanufacturing, notamment les machines tournantes, les crémaillères, boîtes de vitesses, etc. Ce processus de reconditionnement est une étape clé, car il nous permet de redonner une seconde vie à des pièces qui seraient autrement inutilisables. Pour assurer cette activité, le groupe s’appuie sur un "core trader", une entité chargée de regrouper les composants nécessaires au remanufacturing. Cette activité progresse d’année en année, et nous allons notamment de plus en plus loin dans le domaine électronique. Une structure spécifique a été développée à cet effet en Suède, elle s’appelle UBD Cleantech.
Compte tenu des demandes pour cette activité en France, nous allons créer un centre dédié au remanufacturing des équipements électroniques, à l'horizon 2026. Enfin, les composants qui ne peuvent ni être réutilisés ni reconditionnés sont recyclés en matières premières secondaires, grâce à des partenaires broyeurs. Ces matériaux sont ensuite réinjectés dans la chaîne de production pour fabriquer de nouveaux produits, bouclant la boucle de l’économie circulaire.
J2R : Le groupe Autocirc dispose aussi d’une structure spécifique pour la remanufacture des pneumatiques…
M. R. : En Suède, le groupe a, en effet, décidé de dédier une unité au traitement des roues, des pneus et des jantes, pour des raisons de productivité et pour répondre aux besoins des marchés nordiques. Dans ce pays, les demandes en jantes et pneumatiques de réemploi sont effectivement très importantes.
C’est lié notamment à la réglementation qui oblige, comme dans certaines régions en France avec la loi Montagne, à s’équiper en saison hivernale de pneus hiver, voire cloutés. Chez nous, la législation n’étant pas réellement appliquée, ce type de centre n’est pas une priorité. Mais nous restons vigilants, car il n’est pas impossible que le marché évolue avec une application plus stricte de la réglementation.
J2R : Comment le transport des véhicules s’intègre-t-il dans votre modèle ?
M. R. : Le transport est une étape fondamentale dans notre chaîne de valeur. Actuellement, nous utilisons une combinaison de ressources internes et de prestataires externes pour acheminer les véhicules depuis leur lieu de collecte jusqu’à nos centres de recyclage. En Suède, notamment, le groupe dispose de sa propre flotte de transport.
En France, la question se posera très prochainement, car notre approche peut être optimisée en mutualisant ce service. Notre objectif à moyen terme est d’internaliser davantage cette activité en créant une entité dédiée. Cela nous permettrait de mieux contrôler les flux logistiques, de réduire le nombre de camions sur les routes, et donc de limiter notre empreinte carbone. Cette initiative s’inscrit dans notre vision globale d’un modèle durable, où chaque étape du processus contribue à réduire l’impact environnemental.
J2R : En France, quels sont les projets de développement d’Autocirc ?
M. R. : Depuis notre arrivée en France en 2023, nous avons travaillé à structurer un réseau national solide. Nous avons débuté avec l’acquisition de centres VHU à Paris et Saint-Étienne, puis nous avons racheté trois nouveaux sites en 2024. En 2025, nous avons fait l’acquisition d’un centre VHU à Lille. Aujourd’hui, nous disposons de six implantations opérationnelles, principalement dans l’est et le nord de la France. D’ici à la fin de l’année, le groupe devrait passer dans son giron trois à quatre nouveaux sites. En 2026, nous espérons réaliser le même nombre d’acquisitions afin de proposer une couverture nationale avec une quinzaine d’installations.
Objectif : garantir qu’aucun point de collecte ne soit à plus de deux heures d’un centre de recyclage. Cela représente un avantage non seulement écologique, mais aussi logistique. En réduisant les distances entre les points de collecte et les centres, nous pourrons optimiser nos opérations tout en renforçant notre capacité à répondre à la demande croissante en pièces de réemploi. C’est la philosophie du groupe : nous privilégions les "local factories" aux "gigafactories".
J2R : Le recyclage des véhicules électriques représente-t-il un défi particulier ?
M. R. : Les véhicules électriques posent des défis spécifiques, notamment pour la gestion des batteries. Ces composants sont à la fois complexes et dangereux. Nous avons déjà eu des cas où des batteries prenaient feu plusieurs jours après leur arrivée dans nos centres. Nous devons parfois immerger les batteries pour prévenir les risques d’incendie. Cependant, cette méthode n’est pas toujours suffisante pour garantir leur stabilité. Grâce à notre présence dans les pays nordiques, où l’électrification du parc automobile est bien plus avancée, nous avons acquis une expertise solide dans le traitement des véhicules électriques.
Nous comptons notamment un important centre en Norvège qui traite ces modèles. Ces pays nous servent de laboratoire pour développer des solutions adaptées que nous transposons sur d’autres marchés, comme la France.
J2R : Quelles sont les différences entre le marché français et ceux des pays nordiques ?
M. R. : Les pays nordiques ont une longueur d’avance en matière de recyclage automobile. Là-bas, le modèle est très industrialisé et repose sur une collaboration étroite entre assureurs, recycleurs et réparateurs. Par exemple, dans ces pays, les assureurs confient systématiquement les véhicules accidentés aux recycleurs. Et 100 % de ces VHU sont démontés pour produire de la pièce issue de l’économie circulaire. Ce qui permet aux marchés nordiques de garantir un flux constant de pièces de réemploi.
En conséquence, le nombre moyen de pièces démontées par véhicule y est de 40 à 60, contre seulement 20 en France. Sur ce marché, on observe donc une boucle vertueuse entre l’assureur, le recycleur et le réparateur. Chez nous, le modèle est encore en construction. Les volumes confiés aux recycleurs sont plus limités, et une partie des véhicules est revendue pour être réparée à l’étranger, ce qui réduit la disponibilité des pièces pour le marché local. Pour donner un ordre de grandeur, 70 % des VHU sont destinés au recyclage et 30 % du volume est revendu.
Cependant, nous voyons des évolutions positives. Les assureurs sont aujourd’hui très favorables au réemploi qui a deux atouts à leurs yeux : il facilite la baisse du coût de réparation des sinistres et présente des bénéfices environnementaux. Ce qui est sûr, c’est que 2025 sera une année charnière. Les assureurs restructurent leurs réseaux de recycleurs pour favoriser le réemploi, et nous travaillons activement avec eux pour harmoniser les pratiques et développer une filière plus vertueuse.
J2R : Cette approche industrielle du recyclage automobile développée par Autocirc dans les pays nordiques est-elle transposable en France ?
M. R. : Oui, bien sûr. Je suis au cœur de ce mouvement puisque, en tant que dirigeant de la filiale française, j’ai la chance de pouvoir échanger chaque mois avec mes homologues de chaque pays et les équipes de management du groupe. Nous travaillons sur ces sujets afin de pouvoir dupliquer le modèle nordique dans tous les pays. Nous observons les bonnes pratiques et les process vertueux dans chaque marché et essayons de les déployer par la suite. Et à l’inverse, la France peut également être un exemple pour les autres filiales.
Par exemple, dans nos centres stéphanois et lillois, nous avons beaucoup œuvré pour réduire la pénibilité des opérateurs, en installant notamment des convoyeurs automatisés. Les pays nordiques n’en étaient pas équipés et travaillent désormais à installer ces technologies. Le groupe est présent dans plusieurs marchés européens dont l’Allemagne, le Royaume-Uni, la Pologne ou le Portugal.
J2R : Quels bénéfices tirez-vous de cette couverture internationale ?
M. R. : La stratégie du groupe Autocirc repose sur une réponse à la demande européenne, en s’appuyant sur les spécificités de chaque marché. En Suède, par exemple, Volvo est la marque la plus répandue, à l’instar de Renault ou Peugeot en France. Quelques Renault circulent en Suède, mais elles restent rares.
Donc, lorsqu’une Renault sinistrée entre dans un centre de recyclage suédois, seules quelques pièces spécifiques sont démontées, car le marché local n’a pas besoin d’un large panel de composants Renault. En France, les besoins sont totalement différents. Dans le cas d’une Clio 5 recyclée, toutes les pièces sont potentiellement utiles, car cette voiture est largement présente sur les routes françaises. Mais sur une Volvo V60, seules quelques pièces seront extraites, car la demande pour ce modèle est plus limitée.
C’est là que réside l’une des grandes forces d’Autocirc : créer des synergies entre les différents marchés européens. Grâce à notre présence internationale, nous sommes capables d’identifier les besoins spécifiques de chaque pays et de maximiser le démontage des véhicules en fonction de ces demandes. Nos sites adaptent leurs démontages et nous organisons nos flux logistiques en conséquence.
Pour structurer ce fonctionnement, nous allons développer des hubs dans chaque pays. Ils faciliteront le stockage des pièces recyclées et leur distribution efficacement là où elles sont demandées. Ce réseau logistique interpays est l’un des piliers de notre stratégie et montre la valeur ajoutée d’un groupe européen comme Autocirc.
J2R : Autocirc a réalisé toutes ses acquisitions en France au sein du réseau Caréco. Quels liens unissent aujourd’hui le groupe et l’enseigne de centres VHU ?
M. R. : Lorsque Autocirc est arrivé en France, comme dans d’autres pays, la volonté du groupe était claire : créer un maillage national solide en s’appuyant sur les meilleures entreprises du territoire. Cela impliquait de cibler les acteurs les plus performants. En analysant le secteur français, le réseau Caréco s’est naturellement imposé comme un ensemble d’acteurs d’excellence dans le domaine des centres VHU. Aujourd’hui, Autocirc travaille avec des centres issus de ce réseau, mais notre stratégie de croissance externe ne se limite pas à Caréco.
Nos acquisitions dépendent de plusieurs critères : la qualité de l’entreprise, sa typologie, et surtout sa position géographique, pour garantir une couverture homogène et répondre aux besoins locaux de manière efficace. Il est indéniable qu’il existe un lien fort entre Autocirc et Caréco. Ce lien est renforcé par l’implication de la famille Richaud, mais également par la famille Molins, qui a joué un rôle important dans l’aventure Caréco. Aujourd’hui, Autocirc et Caréco cohabitent de manière complémentaire.
Au sein du réseau Caréco, on retrouve à la fois des entreprises appartenant à Autocirc et des centres indépendants. Cette complémentarité repose sur une répartition des rôles bien définie. Autocirc se concentre sur les opérations en "back office" – optimisation des processus, amélioration de la productivité dans les usines – tandis que Caréco joue un rôle de premier plan dans la distribution et la visibilité auprès des clients. Ce partenariat fonctionne également très bien pour les centres qui n’appartiennent pas à Autocirc, mais restent affiliés à Caréco.
Ces indépendants bénéficient de l’image et des services offerts par Caréco, notamment en termes de canal de distribution, d’apport d’affaires ou encore de soutien médiatique. En contrepartie, ils conservent leur autonomie pour gérer leur production et leurs opérations internes. En somme, ce mariage entre Autocirc et Caréco est équilibré et fonctionne à l’avantage des deux parties.
J2R : La filière du recyclage automobile fait face à des évolutions réglementaires importantes, notamment avec la loi Agec et l’obligation de proposer des pièces issues de l’économie circulaire. Quel est votre regard sur ces réglementations ?
M. R. : Elles apportent des évolutions intéressantes, mais elles soulèvent également des problématiques complexes. Nous sommes globalement favorables à ces changements, car ils visent à structurer la filière du recyclage automobile et à renforcer l’économie circulaire. Cependant, il faut reconnaître que ces mesures ont parfois été conçues sans une connaissance approfondie des réalités du terrain. Si je me place sous ma casquette de membre du bureau national de Mobilians, je constate que la volonté du législateur est claire : transférer aux producteurs la responsabilité de la gestion des véhicules hors d’usage, comme cela a été fait pour d’autres secteurs.
Cependant, le recyclage automobile était déjà structuré et fonctionnait bien en France. Les centres VHU agréés géraient efficacement la collecte et le traitement des véhicules en fin de vie. Il n’y avait pas de véritable besoin de bouleverser ce système. Deuxièmement, la spécificité de la filière automobile réside dans la carte grise, qui est un titre de propriété. Contrairement à un frigo ou une télévision, un véhicule est juridiquement rattaché à son propriétaire.
Cette dimension complexifie la gestion des véhicules et ajoute une couche réglementaire unique. Il est également évident qu’une partie de la motivation derrière ces nouvelles réglementations vient de la problématique des filières illégales. De nombreux véhicules échappent encore au circuit légal pour être traités à l’étranger ou par des acteurs non agréés. Malheureusement, ni les systèmes individuels ni les éco-organismes ne résoudront ce problème, car ces filières clandestines continueront d’exister.
J2R : Quelle est la position d’Autocirc face à ces évolutions ?
M. R. : Chez Autocirc, nous avons toujours été en conformité avec la réglementation et, dans bien des cas, nous allons même au-delà des exigences légales. Nous avons signé un accord en France avec l’éco-organisme Recycler mon véhicule, ce qui nous permet de traiter tous les véhicules dans nos centres en respectant les nouvelles règles. Concernant les systèmes individuels, il s’agit d’une autre approche adoptée par certains constructeurs comme Renault, Stellantis, Volkswagen, Ford ou Toyota.
Ces systèmes reposent sur des contrats commerciaux passés directement entre les producteurs et les recycleurs. Lorsqu’un particulier achète un véhicule neuf ou d’occasion chez un concessionnaire du groupe, son ancien modèle est repris. Tous ces VHU constituent un gisement spécifique pour le constructeur, qui peut choisir de le confier à des recycleurs partenaires. Cependant, ces contrats comportent souvent des conditions spécifiques, que ce soit sur les pièces à récupérer ou sur l’exploitation des données issues des véhicules traités.
Ces exigences transforment le système en un véritable partenariat commercial, où chaque partie doit évaluer si les conditions sont intéressantes ou non. Pour Autocirc, ces systèmes individuels représentent une opportunité de travailler en étroite collaboration avec les constructeurs, mais ils ne sont pas indispensables, puisque nous avons déjà un accord avec l’éco-organisme, qui nous permet de gérer tous les véhicules qui entrent dans nos centres.