Le Journal de la Rechange et de la Réparation : Que représente aujourd'hui l'activité recyclage au sein du groupe Derichebourg ?
Thomas Derichebourg : En France, le groupe Derichebourg compte deux grandes filiales. L'une est Elior Group, qui opère dans la restauration collective et les services aux collectivités et entreprises. L'autre, c'est Derichebourg Environnement, qui compte 6 000 salariés, dont l'activité génère un chiffre d'affaires de 3,6 milliards d'euros (dont 3,4 milliards pour le recyclage). Elle est présente dans treize pays : Allemagne, Belgique, Espagne, Canada, États-Unis…
Au total, nous exploitons 290 sites (dont 210 en France) en comptant les filiales de collecte des déchets ménagers, de recyclage des biens de consommation en fin de vie (réfrigérateurs, etc.). On y recycle des métaux ferreux et non ferreux (acier, cuivre, aluminium…), ainsi que de nombreux autres matériaux. Dans le domaine de l'automobile, notre taux de valorisation du véhicule atteint un peu plus de 96 %.
J2R : Quelle est la part précise de l'automobile dans cet ensemble ?
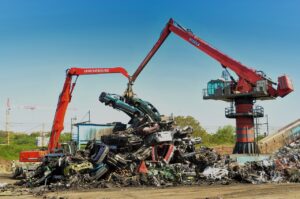
La majorité des véhicules hors d'usage recyclés par Derichebourg Environnement ne sont plus valorisables en pièces de réemploi. ©Derichebourg
T. D. : 160 de nos sites sont agréés pour traiter les VHU [véhicules hors d'usage, ndlr]. 18 d'entre eux disposent aussi d'un agrément d'installation de broyage. Nous y traitons environ 500 000 VHU par an. Dans nos centres de recyclage, les véhicules sont dépollués et démontés. Nous en retirons tous les fluides, les pneumatiques, les hydrocarbures et le vitrage. Chacune de ces matières est stockée dans des contenants appropriés. Elles sont ensuite revalorisées.
Par exemple, les pneus sont recyclés en aires de jeu pour les enfants, ou en CSR (combustibles solides de récupération). Ils remplacent alors les combustibles fossiles, notamment dans les cimenteries.
À lire aussi : Recyclage automobile : vers un essor de la filière illégale ?
Tandis que parmi les fluides, certaines huiles et fluides de climatisation sont régénérés. Puis, ils sont ainsi réinjectés dans la filière en place. Lorsque cela est impossible, ils sont aussi valorisés énergétiquement. Par ailleurs, nous avons mis en place des lignes de traitement spéciales pour atteindre la qualité de combustible requise pour nos partenaires.
J2R : Quel est votre modèle économique, et comment gagne-t-on de l'argent en recyclant un véhicule ?
T. D. : Les véhicules en fin de vie sont collectés ou livrés sur nos sites par les particuliers, garages et centres VHU partenaires. Ensuite, nos technologies de recyclage permettent de produire de nouvelles matières premières que nous revendons à nos clients. Mais il faut déduire les coûts de dépollution de plus en plus élevés.
La puissance de notre groupe réside dans sa taille et sa capacité à valoriser des volumes importants de déchets. Concrètement, le fruit du traitement annuel de 5 millions de tonnes de déchets métalliques (pas uniquement issus des véhicules) représente un chiffre d'affaires non négligeable. Par ailleurs, les cours des matériaux évoluent en permanence, mais nous ne spéculons pas en gardant des stocks. Cela d'abord par conviction et ensuite à cause des risques d'accident – d'incendie essentiellement.
Ensuite, l'un de nos enjeux est également de maîtriser notre impact environnemental. Notre maillage géographique est donc réparti sur tout le territoire national au plus proche des gisements de matières premières en évitant le transport routier. Nous favorisons dès que possible le transport fluvial.
À lire aussi : Recyclage des batteries de VE : la course à l’économie circulaire est lancée
Surtout, pour rentabiliser notre activité, il faut recycler au maximum, sans oublier les matériaux plus difficiles à revaloriser. C'est la raison pour laquelle nous améliorons constamment nos procédés. Par exemple, lors du recyclage d'un véhicule, la présence de petits moteurs électriques en acier contenant des bobines de cuivre représente un défi important. Mais nous parvenons à séparer les deux métaux, ce qui nous apporte de la valeur, alors que le cuivre est un polluant pour les aciéristes.
Maintenant, à partir de ces moteurs, nous produisons de la grenaille de cuivre avec un taux de pureté de plus de 99 %. Cela vaut donc la peine d'innover pour capter tous ces fragments de cuivre. Raison pour laquelle notre service de recherche et développement travaille sur ces sujets.
J2R : Produisez-vous aussi de la pièce de réemploi (PRE) ?
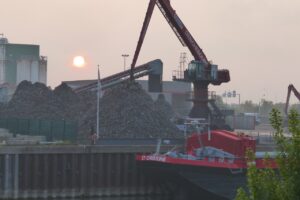
Le site du port de Gennevilliers (92) en bord de Seine fait partie des sites Derichebourg recourant au transport fluvial. ©Derichebourg
T. D. : Non, nous ne produisons pas de PRE. Nos centres VHU reçoivent 70 000 à 80 000 véhicules à dépolluer par an. Ils sont généralement âgés de 19 à 20 ans, quand l'âge moyen du parc roulant est de près de douze ans. Leur potentiel en pièces d'occasion reste faible. Globalement, nos VHU sont donc plus âgés que ceux destinés à la production de PRE.
Cependant, nos installations de broyage travaillent aussi avec des centres VHU externes producteurs de PRE. Ils nous approvisionnent en carcasses, une fois que les pièces d'occasion en ont été retirées. Nous restons néanmoins attentifs à cette activité et sommes d'ailleurs aussi actionnaires de deux spécialistes de la PRE : Allo Casse Auto et la Dac.
J2R : À côté de ces véhicules anciens, êtes-vous confrontés aux motorisations électriques ?
T. D. : Dans ce domaine non plus, nous ne traitons pas encore les véhicules électriques, car les seuls arrivant en fin de vie sont accidentés. Ils peuvent donc être encore utilisés pour produire de la PRE. Par ailleurs, les véhicules sinistrés – dont les VE – sont gérés par les réseaux d'assurance. Or, nous n'avons aucun contrat avec eux pour l'instant.
Le coût de la dépollution est de plus en plus élevé
Mais nous réfléchissons dès maintenant à la problématique des véhicules électriques avec leurs spécialistes, car nous devrons recycler leurs batteries lorsqu'elles arriveront en masse dans nos centres. En attendant, nous prenons en charge depuis longtemps les batteries classiques au plomb.
J2R : Quelles sont vos limites, notamment les 4 % de matériaux d'une voiture que vous ne parvenez pas à recycler ?
T. D. : Il s'agit essentiellement de certaines mousses de sièges, tissus, et tapis en PVC. Car ces matériaux contenant du chlore ne peuvent pas être revalorisés en CSR. Ils ne sont pas non plus recyclables et finissent souvent en installation de stockage. Encore une fois, notre R&D représente d'énormes enjeux pour nous. Elle nous a permis d'améliorer notre qualité sur les polypropylènes (des pare-chocs et batteries) déjà valorisés.
Parallèlement, nous entretenons des partenariats avec des plasturgistes pour mettre en place une boucle fermée dans l'automobile. Finalement, on peut comparer le recyclage à un régime alimentaire destiné à maigrir. Les premiers kilos sont les plus faciles à perdre, et les derniers les plus difficiles.
J2R : A contrario, quels sont vos domaines d'excellence en matière de recyclage ?
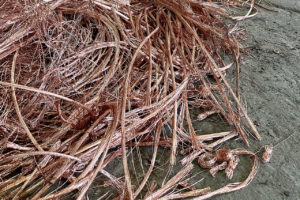
Le service de recherche et développement de Derichebourg Environnement a notamment permis au recycleur d'améliorer au mieux la qualité de son cuivre recyclé. ©Derichebourg
T. D. : Dans le domaine de l'aluminium, comme pour le cuivre, notre process est très abouti. Nous disposons de nos propres affineries pour produire des lingots que nous revendons à l'industrie. Nous sommes aussi parvenus à reproduire les mêmes performances pour les batteries au plomb. Nous parvenons à les recycler à 96 ou 97 %. Leur acide est neutralisé et transformé en chlorure de sodium. Ce sel est revendu aux secteurs qui l'emploient.
Le plomb est également recyclé et commercialisé. Nous atteignons ainsi pour les batteries le même taux de recyclage que pour le véhicule global.
J2R : Et où en êtes-vous pour l'acier ?
T. D. : Dans le domaine des métaux, nous alimentons les sidérurgistes avec notre production. Nous comptons améliorer sa qualité à l'avenir, suivant les exemples de nos savoir-faire pour le cuivre et l'aluminium. En effet, actuellement les aciers sortant de nos lignes ne peuvent pas resservir pour l'automobile. Mais ils peuvent être réutilisés dans le BTP, sous forme de fer à béton pour renforcer les constructions, ainsi que pour d'autres applications. Nous espérons en tirer un avantage concurrentiel dans le futur.
Nous réfléchissons à la problématique des véhicules électriques
J2R : Derichebourg Environnement communique sur ses engagements en matière de responsabilité sociétale et environnementale (RSE). Au-delà de votre activité de recyclage, quelles sont vos pratiques internes ?
T. D. : Fondamentalement, toutes nos activités sont réalisées par des femmes et des hommes qui occupent des emplois non délocalisables. Je crois qu'il s'agit là de la force de Derichebourg Environnement. Il n'existe pas d'école de recyclage pour apprendre à dépolluer et à valoriser des matières.
Ce métier s'apprend d'abord sur le terrain. Et ce sont nos salariés, sur tous nos sites, qui détiennent localement ces savoir-faire. Ils savent exactement comment on traite, on sépare, on valorise. Nous les formons aussi sur l'incendie, les gestes et postures, etc. Nous nous appuyons donc sur un pôle RH conséquent, car nous sommes une grande équipe, une grande famille. Nous sommes une entreprise internationale, qui demeure cependant toujours familiale.
ENCADRÉ
Quand Derichebourg Environnement prépare l'avenir
Si les recycleurs automobiles parviennent à revaloriser l'intégralité des véhicules, ils espèrent, dans un avenir proche, pouvoir valoriser la totalité de leurs matériaux. Les équipes R&D de Derichebourg Environnement étudient donc notamment les améliorations possibles de leurs procédés de dépollution, de tri et de collecte de matériaux.
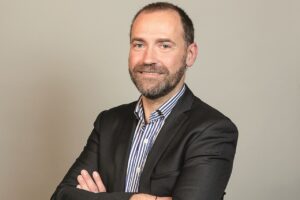
Sébastien Paul, coordinateur QSE et responsable RSE de Derichebourg Environnement. ©Derichebourg
"Nous avons du mal à récupérer les aimants permanents, cite en exemple Sébastien Paul, coordinateur QSE et responsable RSE de Derichebourg Environnement. Ce sont de toutes petites quantités de métaux très rares que l'on retrouve dans les enceintes acoustiques et les colonnes de direction. Ces aimants sont installés dans des endroits difficiles d'accès. Parfois ils sont ferriques, très pauvres et sans grande valeur. Dans les années à venir, nous allons donc industrialiser ce process spécifique. Les process d'extraction de ces éléments devront donc être industrialisés. Pour l'instant, les recycleurs observent où les prélever en plus grand nombre pour se focaliser sur les équipements à cibler… Cela pourrait ainsi commencer par l'électroménager."
Autrement, le groupe collabore directement avec les constructeurs automobiles et les équipementiers pour répondre aux mesures progressivement imposées par les nouvelles réglementations françaises et européennes sur la recyclabilité des véhicules. "Nous travaillons déjà avec Renault et Stellantis pour les différents métaux et matières, sans attendre la nouvelle organisation de la filière VHU. D'autres partenariats vont encore se mettre en place, pour répondre aux besoins d'incorporation de matière recyclée de qualité dans les futures voitures, annonce Sébastien Paul. Actuellement, nous menons des études en lien avec les adhérents de Federec – dont nous faisons partie – et Forvia sur le potentiel des mousses automobiles. Nous travaillons aussi avec d'autres équipementiers sur la réintégration du plastique recyclé dans les pare-chocs…"
À lire aussi : Mobilians encadre le recyclage des véhicules électriques
Ces travaux concernent aussi d'autres niches comme les joints. Tout est bon pour intégrer de la matière recyclée et recyclable dans l'auto. Parmi les autres projets figure aussi le traitement des batteries de véhicules électriques. Mais cette activité présente encore de sérieux défis techniques. "Avant de les prendre en charge, nous devons mettre en place un process industriel spécifique, rappelle Thomas Derichebourg. Or, celui-ci reste pour l'instant très compliqué à fixer, car les technologies de ces batteries évoluent presque tous les jours, avec des gains d'autonomie très importants. Leurs fabricants trouvent sans cesse de nouveaux composants… Par ailleurs, une autre inconnue demeure sur la seconde vie de ces batteries. Certains étudient par exemple leur réexploitation dans le secteur photovoltaïque, pour stocker de l'énergie. Il est donc encore trop tôt pour nous."
Le dirigeant estime qu'il faudra attendre quinze à vingt ans avant de voir arriver les VE dans ses centres. Entretemps, des progrès auront donc été réalisés sur bien d'autres postes.